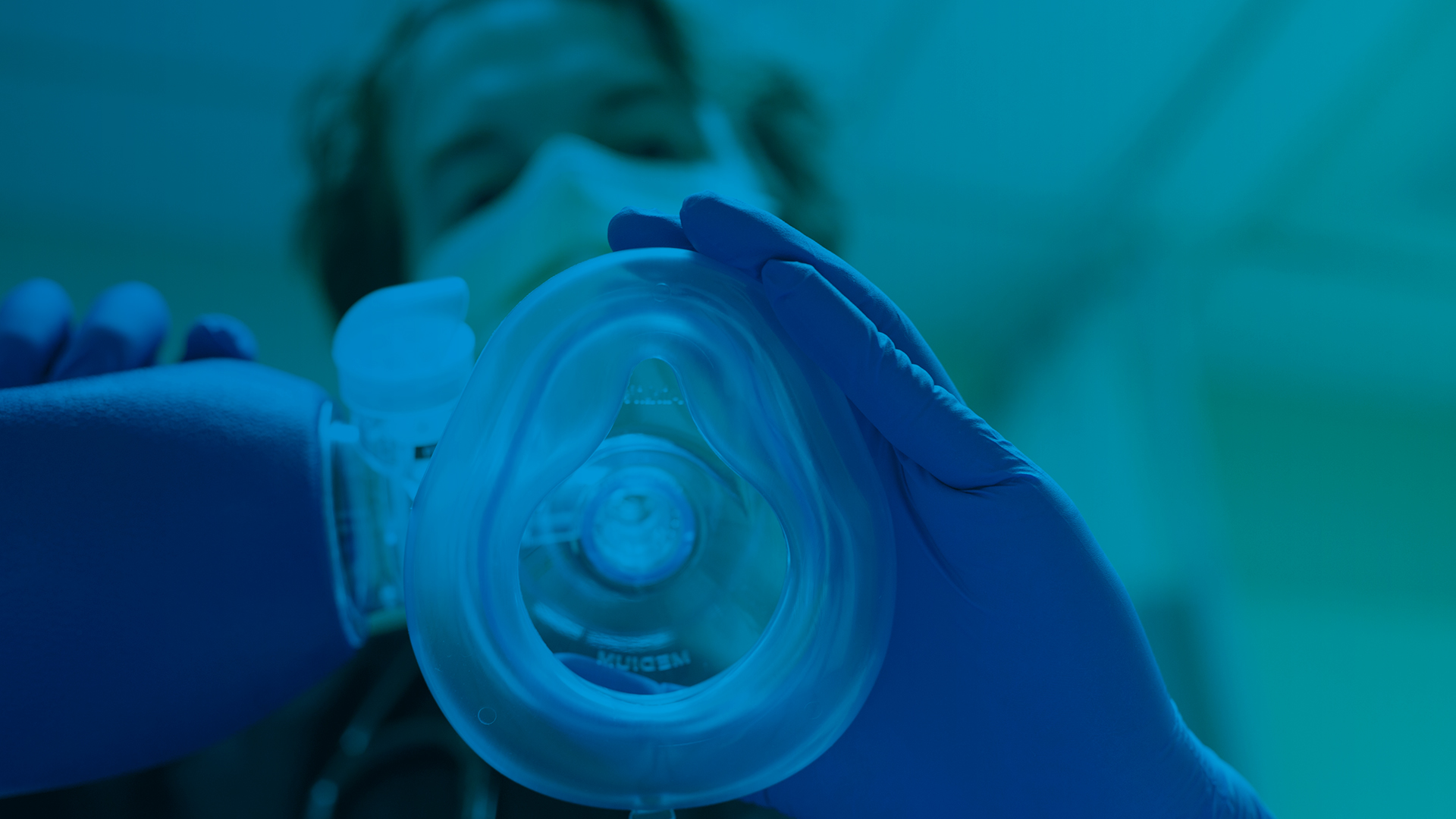
Liquid Silicone Rubber (LSR)
Liquid Silicone Rubber (LSR) is a versatile material known for its high precision and durability. It is often used in industries where complex parts with fine detail, tight tolerances and low shrink rates are required.
It is ideal for producing medical devices and seals due to its excellent biocompatibility and resistance to extreme temperatures, chemicals, and UV light.
LSR is commonly used in the production of medical and personal healthcare devices, including face masks, T-seals, O-rings and period cups. Its properties make it suitable for creating components that require high precision and durability.
At Pact NZ, we leverage the latest global technology to enhance resin performance, ensuring that our Liquid Silicone Rubber (LSR) is specifically designed for injection moulding processes to produce high-quality medical parts and devices. Our accredited LSR supply meets both EMA and USFDA approval standards, guaranteeing the highest level of safety and reliability.
Latest Global technology for improved resin performance
Liquid Silicone Rubber specifically made for injection moulding processes to produce medical parts and devices.
Accredited LSR supply which allows for both EMA and USFDA approval.
Liquid colour designed for use with LSR.
Concentrates are formulated with colour-stable, highly compatible ingredients evaluated to the highest Industry standards.
The Liquid Silicone Rubber Process:
Annealing:
The annealing process involves heating the finished product in an industrial oven at 200˚ C for four hours. This step ensures that the material surface is fully cured, promoting improved barrier protection and extending the product’s lifespan. Additionally, the cured surface significantly reduces any staining, enhancing the overall quality and durability of the product.
Over Moulding:
In the over moulding process, all individual components are first injected, and then the silicone is over moulded to complete the finished product. This method ensures a seamless integration of parts, resulting in a high-quality, durable final product.
Assembly:
Our manual assembly area is dedicated to closure affixment and labelling. This step ensures that each product is meticulously finished and ready for use, meeting the highest standards of quality and precision.
Contact Us
Please fill in the form below and someone will be in touch with you shortly.
This site is protected by reCAPTCHA and the Google Privacy Policy and Terms of Service apply.